Zpracování PUR pěn
Z historie polyuretanu
Polyuretan má svou historii z doby před 2. světovou válkou. Centrem výzkumu bylo město Leverkusen v Německu u firmy BAYER. V roce 1937 profesor Otto Bayer (1902-1982) a jeho tým zjistili, že reakce alifatických diisokyanátů a alifatických dipolyolů vede ke vzniku lineárních polymerů s vysokou molekulovou hmotností. Tyto polymery, pojmenované poté polyuretany, které měly velmi zajímavé vlastnosti pro výrobu umělých hmot a vláken, byly uvedeny na trh v Německu pod obchodními názvy Igamid a Perlon v roce 1942.
Dalšími významnými osobnostmi, podílejícími se na procesu tvorby polyuretanu, byli američtí vědci Dr. William "Butch" Hanford a Dr. Donald Fletcher Holmes. V roce 1942 objevili skutečnost, že di-isokyanáty a stávající polyoly se dají sloučit velmi rychle, narozdíl od původní (časově zdlouhavé a finančně nákladné) německé metody. Tento objev umožnil nastartovat výrobu polyuretanů ve větším měřítku a za nižší cenu.
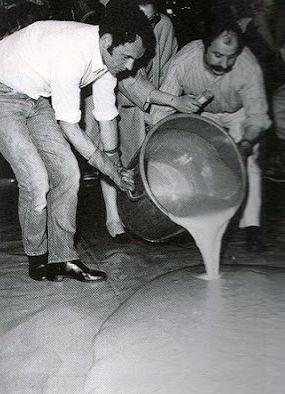
Hanfordova věta "vývoj tohoto vynálezu mi trval sedmnáct minut" se stala známou i vzhledem k faktu, že především rychlost reakce byla důležitou částí tohoto objevu. Jejich postup se používá dodnes pro výrobu většiny polyuretanových systémů. V roce 1953 Dr. Bayer navázal spolupráci s firmou Monsanto Chemical Company a vznikla společná firma MoBay Chemical Corporation pro výrobu umělých hmot v USA. Skutečný rozmach polyuretanů nastal v roce 1957 především díky použití nových typů polyolů na bázi polyéterů. Velká variabilita těchto polyolů umožnila výrobu širokého spektra nových polyuretanových systémů tak, jak je známe i dnes.
K rychlému rozšíření polyuretanových systémů došlo nejen díky jeho vynikajícím vlastnostem, ale také díky spolupráci a vývoji třech odlišných oborů:
- chemický průmysl vyvinul a dodává suroviny včetně návodu na jejich zpracování s parametry výsledné PUR pěny (tzn. že při dodržení podmínek zpracování stanovených výrobcem docílíme deklarovaných vlastností)
- strojírenský průmysl vyvinul a dodává strojní zařízení, která splňují požadavky na zpracování surovin a umožňují vznik produktu - PUR pěny
- zpracovatelé, kteří sami vyrábějí z dodávaných surovin pomocí vhodného zařízení výsledný výrobek - PUR pěnu. Tato výroba má různé formy a podoby tak jak je zmíněno dále. Znalost chemické a chemicko-fyzikální podstaty je významná pro zpracovatele PUR k pochopení všech závislostí a důsledků.
Typy polyuretanů
Zpracovávané polyuretanové systémy můžeme z hlediska jejich uplatnění rozdělit na následující typy konečných výrobků
- tvrdé pěny
- integrální pěny
- měkké pěny
- elastomery
- barvy
- těsnění
- lepidla
- jednosložkové a dvousložkové pěny v tlakových nádobách
V průmyslu a stavební výrobě se uplatňují díky svým výborným izolačním a fyzikálně technickým vlastnostem různé typy PUR pěn. Z těchto pěn je to především tvrdá PUR pěna s uzavřenou strukturou buněk, která je zpracovávána do konečného výrobku následujícími technologickými postupy (aplikacemi):
- litím
- nástřikem
- nástřikem „na místě“ (in sito)
Chemická podstata PUR pěny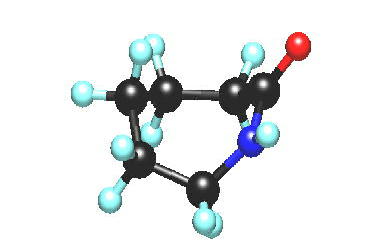
Výchozími surovinami pro plasty obecně jsou např. zemní plyn, uhlí, ale především základní a nejvýznamější surovina - ropa. Plasty jsou organické sloučeniny, které obsahují především uhlík, dusík, síru a chlor. Jsou lehké a převážně dostatečně odolné povětrnostním vlivům. Výroba plastických hmot probíhá pomocí chemické reakce, který se obecně nazývá syntéza. Existují tři 3 základní typy syntézy
- polykondenzace - např. PA (polyamid)
- polymerizace - např. PE (polyetylen), PVC (polyvinylchlorid), PS (polystyren)
- polyadice – např. PUR (polyuretan)
Základem syntézy polyuretanových pěn je reakce izokyanátů (látky obsahující chemicky reaktivní skupiny – NCO), polyolů (polyalkoholů), aminů a vody (látky obsahující hydroxylové skupiny a aminové skupiny -OH, -NH2). Volbou vhodné kombinace látek vstupujících do reakce lze získat polyuretany s různými vlastnostmi (od velmi „pružných“ elastických pěn až po „silně zesíťované“ tvrdé pěny.
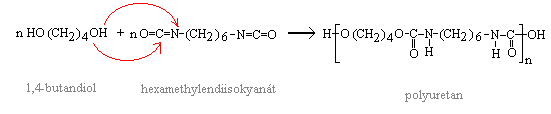
Reakce při níž polyuretan vzniká je exotermní a rychlost průběhu reakce závisí
-
na druhu použitého polyolu, popř. aminu a izokyanátu
-
na jejich koncentraci v reakční směsi
-
na teplotních podmínkách
-
napřítomnosti dalších látek ovlivňujících průběh reakce (např. katalyzátory)
Průběh reakce při vzniku PUR pěny
Proces „vypěňování“ začíná vývinem nadouvacího plynu. Tímto plynem může být buď CO2 (uvolněný chemickou reakcí izokyanátu s vodou) nebo inertní látka freon R-XX, který se při vzrůstu teploty nad jeho bod varu mění na plyn, aniž by předtím chemicky reagoval. Předpokladem pro začátek napěňování je přesycenost reakční směsi plynem a dostatek zárodečných center pro vznik bublin. V dalším průběhu reakce se objem bublin, které mají přibližně kulovitý tvar zvětšuje až do objemové hmotnosti pěny cca 250 kg/m3. V této fázi se začínají bubliny dotýkat a deformovat, zvláště ve směru růstu, až při zatuhnutí vytvoří stabilní systém polyedrických buněk, jejichž stěny jsou vlastně tenké membrány.
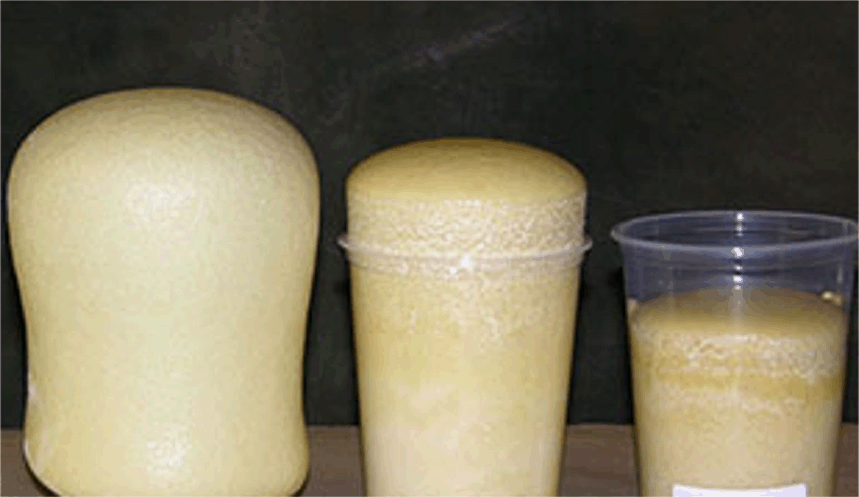
Příprava PUR pěny je tedy složitý chemický a fyzikální proces. Pro dosažení určitých vlastností PUR pěn je nutno k reagujícím složkám přimísit pomocné a přídavné látky, které ovlivňují jejich výslednou podobu. Toto pro zpracovatele a aplikátora PUR pěn na stavbě téměř neproveditelné. Proto v dnešní době připravují výrobci dvousložkové systémy již s konkrétními vlastnostmi pro danou aplikaci a polyolová složka (jako méně reaktivní látka) obsahuje všechny tyto „pomocné“ látky.
Typy PUR pěn a jejich složení
Pro nástřiky a lití se v praxi používají dvousložkové systémy pur pěn, které se liší svými vlastnostmi (např. objemovou hmotností, startovacími časy, směšovacímí poměry, výslednými fyzikálně technickými vlastnostmi , apod.). Jednotlivé složky systémů PUR pěn tvoří
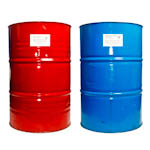
složka A (obecně izokyanát s tmavě hnědým zabarvením) obsahující
- homogenizovanou směs izokyanátů
složka B (obecně polyol s bledým či žlutohnědým zabarvením) obsahující
-
homogenizovanou směs polyolů
-
nadouvadlo nebo směs nadouvadel
-
stabilizátory pěnění
-
aktivátory (katalyzátory) pěnění a síťování
-
aditiva (retardéry hoření, antioxidanty, pigmenty apod.)
Recept „know-how“ má výrobce surovin a na zpracovateli zůstává druhá část procesu tzn. na místě smísit obě dvě složky za podmínek a ve směšovacím poměru daném výrobcem a vytvořit finální výrobek.
Zpracovatel přebírá záruku za pěnu, vyrobenou na místě aplikace, protože její vlastnosti a kvalita závisí do značné míry na postupu, okolních podmínkách, použitém zařízení a samotných pracovnících.
Základní způsoby zpracování PUR pěn
Při výrobě polyuretanových pěn se používají tyto základní technologické způsoby výroby
- lití do meziprostoru nebo otevřených forem (volné lití)
- lití do uzavřených forem vstřikováním (tlakové lití)
- injektáže
- nástřiky
Technologie lití do meziprostoru nebo otevřených forem (volné lití)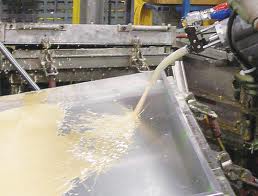
Tohoto způsobu se používá především u velkoprostorových izolací jako jsou zásobníky, nádrže, energetické kanály a jiné mezistěnové izolace. Nejčastěji se provádí jako lití po vrstvách tak, aby nedošlo k deformacím nebo k poškození PUR pěny vysokou koncentrací reakčního tepla. U této technologie se používají systémy obvykle s nižší objemovou hustotou cca 30-40 kg/m3.
Technologie lití do uzavřených forem (tlakové lití)
Tento způsob se uplatňuje především při sériové výrobě izolačních prvků, u kterých se požaduje přesný rozměr a vysoká kvalita povrchu spolu s dobrými mechanickými vlastnostmi. K lití se používají systémy PUR pěny o objemové hustotě 30-250 kg/m3. Použité nadouvadlo je nejčastěji na bázi CO2. Nejrozšířenější uplatnění této technologie je ve výrobě izolačních panelů sendvičové konstrukce ve stavebním a automobilovém průmyslu. Do uzavřené formy se nadávkuje přesně stanovené množství systému PUR. Celková doba vypěnění a vyzrání PUR pěny ve formě je určena reaktivitou použitého systému a pohybuje se obvykle v rozmezí 15-30 minut.
Technologie injektáže
Tato speciální technologie se používá především pro zpevňování hornin nebo zdiva, utěsňování stavebních konstrukcí proti průnikům tlakové vody (tunely, podzemní stavby, hráze vodních děl, důlní konstrukce, apod.). Princip injektáže PUR spočívá obvykle v předvrtání potřebného množství otvorů v místě aplikace, do kterých jsou upevněny speciální injektážní trysky. Injektážní PUR systém je po připojení vysokotlakého čerpadla na tyto injektážní trysky vháněn pod vysokým tlakem až do místa injektáže, kde účinkem reakce složek dojde k následnému zpevnění a zatěsnění injektované části stavby. U injektáží staveb proti tlakové vodě se používá speciálních systémů PUR, u kterých k nadouvací reakci dochází až při přímém kontaktu s vodou.
Technologie nástřiku PUR pěn " na místě" (in sito)
Zpracování PUR pěny stříkáním na místě patří k nejmodernějším, ale současně k nejnáročnějším způsobům vytváření tepelných a vodotěsných izolací. PUR pěna vzniká přímo na místě směšováním dvou tekutých složek, které se na podklad nanášejí stříkáním. K nástřiku PUR pěn se používá speciální vysokotlaké zařízení se směšovací pistolí. Pěna se v průběhu reakce, která trvá několik sekund, spojí trvale s podkladem a po několika minutách zreaguje na nelepivou vrstvu.
Hlavními efekty této technologie jsou především
-
velmi dobré hodnoty fyzikálních a mechanických vlastností
-
vysoký výkon při aplikaci PUR pěny
-
jednoduchá technika nanášení
-
bezespárové provedení a vodotěsnost v celém průřezu PUR pěny
-
vysoká užitná hodnota především ve stavební výrobě při provádění tepelných izolací, tepelných a vodotěsných izolačních vrstev (krytin)